Precision Products
We are material designers, manufacturers, and producers—delivering complex geometries and innovative applications of superior quality with less waste.
“Synergy makes us efficient. We offer the ability to make assemblies and sub-assemblies with components from our stamping, powdered metal, and cold forming operations—all under one roof.” - Brian Dalisay, Engineering Manager.
Key Solutions
Driving Innovation
Scaling efficiencies for industrial leaders.
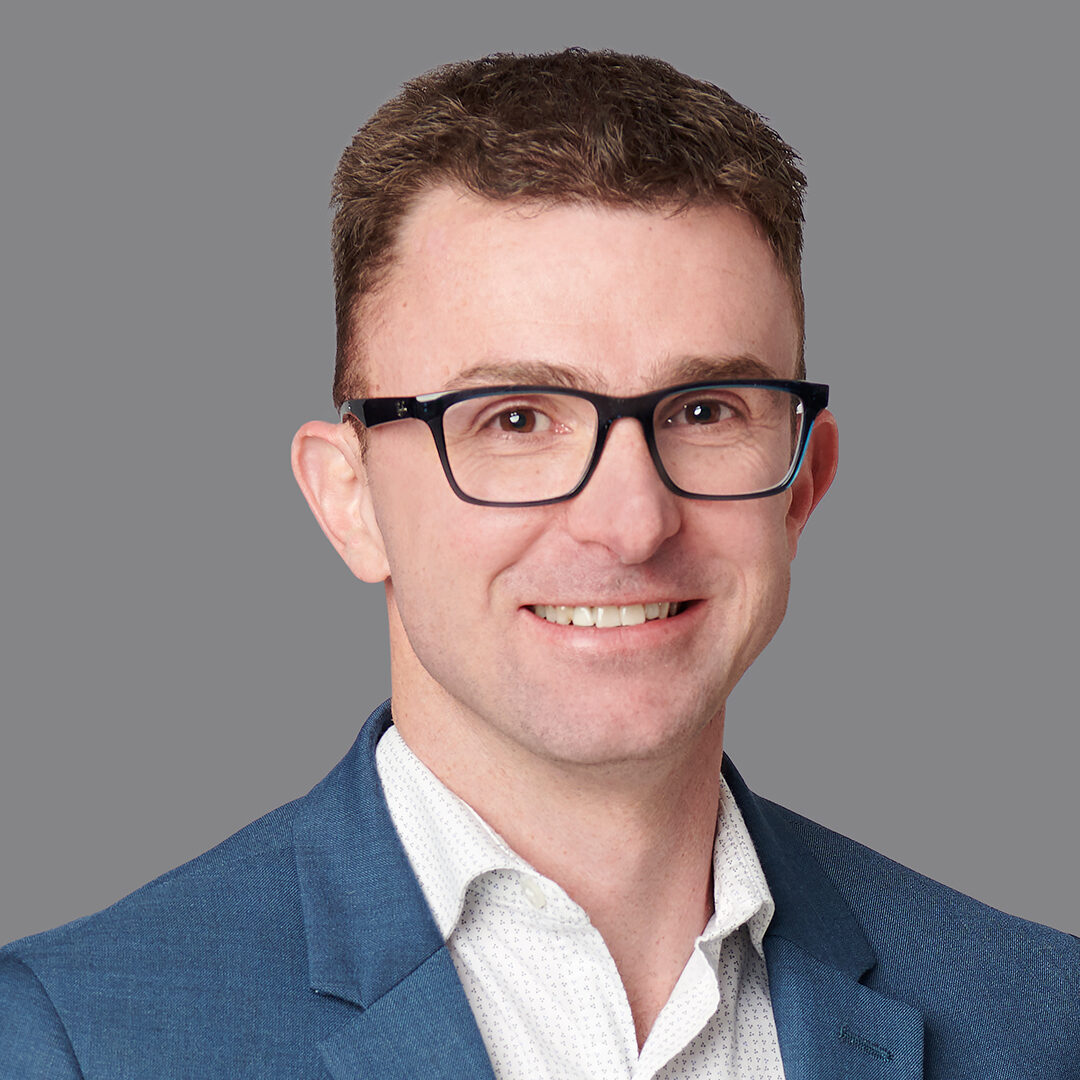
Technical Applications Manager
Brad Holmes
“The collaborative culture across all the different business units is exciting and it provides opportunities to elevate and scale best practices across our capabilities.”
Key Applications
Power. Precision. People. That’s the Amsted difference.
“We look at innovation differently. It’s not only product innovation. It’s process innovation. It’s people innovation. And looking at how to leverage innovation to maximize value for our customers.”
Keith Johnson, VP of Global Operations